
Supplied: 20,000 Vibration Isolation Pads
Cambridgeshire Guided Busway
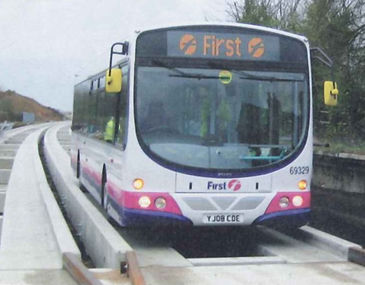
The Cambridgeshire Guided Busway is a guided bus system that will use a disused railway line from St. Ives to Cambridge, with an additional section operating between the railway station and a Park & Ride scheme. At 25 km long, the busway will be the longest in the world. The Guided Busway is made from pre-cast concrete. Due to the vast amount of pre-cast concrete beams required Edmund Nuttall set up their own plant to cast the beams at Longstanton. The nearest company which could cope with the manufacture requirement was over 200 miles away so transportation alone would have cost millions. Therefore it was more economic to build a plant near to the site.
It is estimated that 11,500 journeys a day will be made on the busway. It is intended to help to ease congestion on the busy A14, which links Huntingdon and Cambridge, and provide an alternative and convenient mode of transport for car users in the area. The route will pass through the proposed new town of Northstowe, a significant area of urban development which will accommodate around 10,000 new houses. The council weighed up the various schemes, heavy train system, tram system, and guided busway system, and found that the guided busway would be the best option.
Transporting these beams around Cambridge would have been very difficult at 15 metres long and 2.6 metres wide, weighing around 32 tonnes. A special crane was developed which was used to pick the beams up once they had been cast, and then using the guided busway they were transported to their final destination. This design enables heavy goods transportation on the roads of Cambridge to be kept to a minimum thus restricting inconvenience on current traffic.
Job Brief
Background Information
Project Team
Client: Cambridgeshire County Council
Consulting Engineers: Arup
Main Contractor: Edmund Nuttall Ltd
Start Date: March 2007
Completion Date: 2009
Rubber Pads
Ekspan provided the vibration isolation pads for the scheme, a total of 20,000 pads were moulded especially to suit the extremely tight tolerances provided by our client¡¯s consultan Arup. These pads are placed at the ends of every beam (as indicated below). The rubber we used was manufactured in accordance with BS5400 and had a shore hardness of 60 (+/-5mm).
Ekspan's Solution